La ligne de production de poudre prémélangée entièrement automatisée pour ce projet est conçue pour produire 300 000 tonnes de sucre prémélangé par an. Il s’agit principalement d’une poudre finie fabriquée en mélangeant 90% de sucre, d’amidon et d’autres additifs via un système d’ingrédients. Ses principales propriétés sont les additifs alimentaires auxiliaires, les aliments / boulangerie / gâteaux / boissons solides / café / thé au lait / pain / dessert / pâtisserie en poudre prête à l’emploi.
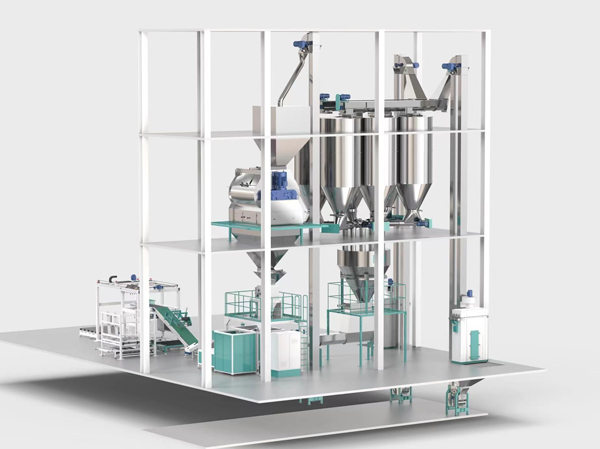
Ligne de production de poudre prémélangée entièrement automatique
Capacité de traitement: 50 – 2000 tonnes / jour
Champ d’application: matériaux granulaires et en poudre
Présentation du produit: céréales, farine, amidon, canne à sucre, sucre blanc, Glucose en poudre mélangé proportionnellement
Sur demande, deux ou plusieurs matériaux sont mélangés avec d’autres additifs dans une certaine proportion à travers un système de dosage pour former une poudre finie. Ses principales propriétés sont les additifs alimentaires auxiliaires, les poudres prémélangées pour aliments / boulangerie / gâteaux / boissons solides / café / thé au lait / pain / desserts / pâtisseries.
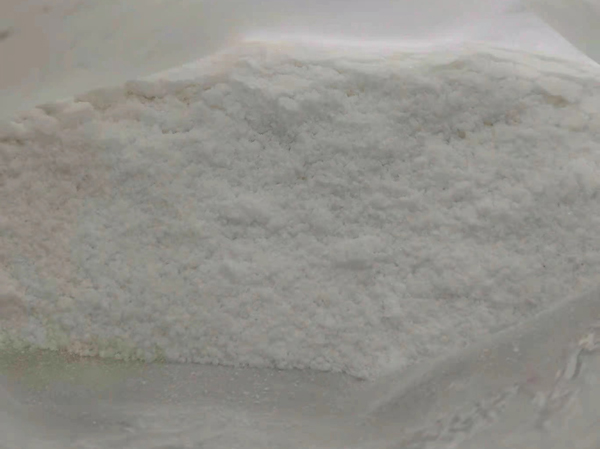
La ligne de production de poudre prémélangée de la zone de stockage est conçue, fabriquée et construite par la société, principalement en utilisant un système d’ingrédient informatique pour mélanger avec précision les matières premières principales et les matériaux auxiliaires, mélanger uniformément pour faire la poudre prémélangée finie et l’utiliser comme additif pour les matériaux auxiliaires alimentaires.
Toute la ligne de production est construite dans l’usine standard existante, divisée en un atelier de purification de l’alimentation en matières premières, un atelier de traitement du mélange de poudre prête à l’emploi et un atelier de stockage des emballages finis. Les principaux équipements de traitement sont installés sous la forme d’une plate – forme à cadre en acier. L’atelier de traitement du mélange des ingrédients couvre une superficie de 11x7m et une hauteur d’environ 14M. L’atelier de purification des matières premières couvre une superficie de 100 mètres carrés et la ligne de palettisation d’emballage entièrement automatique couvre une superficie de 12x5m.
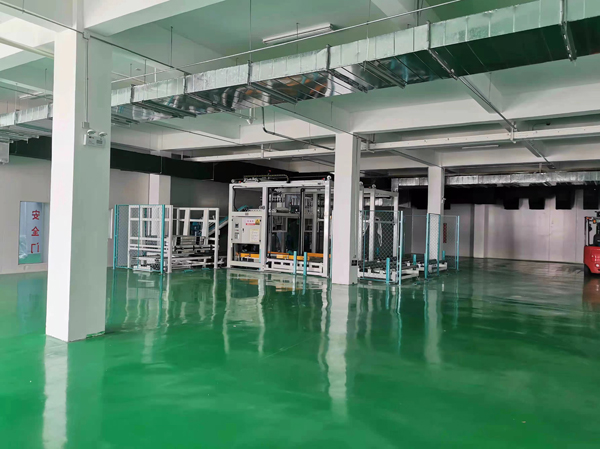
Les matières premières principales, telles que le sucre blanc et les matériaux auxiliaires, sont introduites dans des tubes sans soudure en acier inoxydable via une vanne d’alimentation fermée après avoir été introduites dans la plate – forme d’alimentation de l’atelier de purification. Ils sont ensuite transportés dans le bac de dosage par transport pneumatique de dilution sous pression négative. Adopte le processus de pesage automatique des ingrédients, contrôlé par ordinateur, les ingrédients sont précis, le degré d’automatisation est élevé et économise de la main – d’œuvre; Une fois le dosage terminé, afin de réduire la hauteur de l’étagère, il est à nouveau stocké temporairement dans un bac de mélange à l’aide d’un transport pneumatique de dilution sous pression négative, puis mélangé dans un mélangeur. Le produit fini mélangé uniformément tombe directement et entre dans le processus d’emballage. La ligne d’emballage entièrement automatique est utilisée pour l’ensachage, le pesage, la couture et le scellement automatiques. Enfin, le palettiseur à position haute palettise automatiquement les produits et le chariot élévateur achemine les produits vers la zone de palettisation des produits finis.
L’ensemble du processus de production est concis et clair, avec un degré élevé d’automatisation, ce qui réduit le coût de la main-d’œuvre de l’entreprise et améliore l’efficacité économique; Le matériau est transporté en utilisant un transport pneumatique à pression négative, qui n’a aucun résidu ou contamination croisée, et est pratique pour le nettoyage des pipelines, améliorant l’hygiène et la sécurité de la production.
1, matière première recevant la section
Stocker les matières premières requises pour la production dans l’atelier d’alimentation de purification à l’avance. Pendant la production, chaque matière première est introduite dans la trémie d’alimentation selon les exigences de la formule et envoyée dans le pipeline sans soudure en acier inoxydable par un distributeur d’air fermé. Le matériau est ensuite pompé vers le bac de dosage désigné par un ventilateur à racines.
2, section d’ingrédient
Une fois les matériaux entrés dans le bac à dosage, le système de dosage les décharge automatiquement dans l’ordre suivant la formule, contrôlée par le programme de dosage, et entre dans l’échelle de dosage pour la mesure. L’ensemble du processus est contrôlé par un ordinateur. L’erreur d’exactitude de dosage dynamique du système de dosage est ≤ 3 ‰, et l’erreur d’exactitude statique est ≤ 1 ‰, avec la haute précision et l’efficacité.
3, section de mélange
Afin de réduire la hauteur de toute la ligne de production, les matériaux sont acheminés vers le bac de mélange par un transport pneumatique à pression négative une fois le dosage terminé, puis entrent dans le mélangeur à lame monoaxe en acier inoxydable pour le mélange. Le temps de mélange du mélangeur est environ 120-300 secondes (le temps spécifique est ajusté selon différentes formules), et l’uniformité de mélange est ≥ 95%.
4, section d’emballage de produit fini
Les matériaux mélangés entrent dans le système d’emballage, qui est une ligne d’emballage entièrement automatique avec ensachage, pesage, couture et scellage automatiques. Enfin, un système de palettisation automatique de haut niveau est utilisé, et les produits sont transportés vers la zone d’empilage du produit fini par chariot élévateur.
5, section auxiliaire
Dépoussiérage d’atelier: après que l’alimentation et le dosage de matière première soient terminés, ils entrent dans le mélangeur et sont tous transportés par le système pneumatique de transport de pression négative, sans débordement de poussière; La zone d’emballage est également équipée d’une hotte d’aspiration pour le dépoussiérage.
La zone de l’équipement est entièrement fermée et séparée, et le personnel doit subir une douche d’air et une purification avant d’entrer dans la zone de traitement de l’équipement; Après l’alimentation, les matières premières doivent être nettoyées en temps opportun et le système de transport doit être maintenu inactif pendant plus de 2 minutes pour s’assurer que les diverses matières premières ne contaminent pas pendant le processus de transport.