Avec l’augmentation constante du nombre de voitures en Chine, le traitement des pneus usagés est devenu un sujet de protection de l’environnement, qui a également donné naissance à un certain nombre d’équipements de raffinage des huiles de pneus usagés. À l’heure actuelle, il existe trois formes principales d’équipement de raffinage des pneus usagés sur le marché national : l’équipement de raffinage intermittent, l’équipement de raffinage semi-continu et l’équipement de raffinage continu.
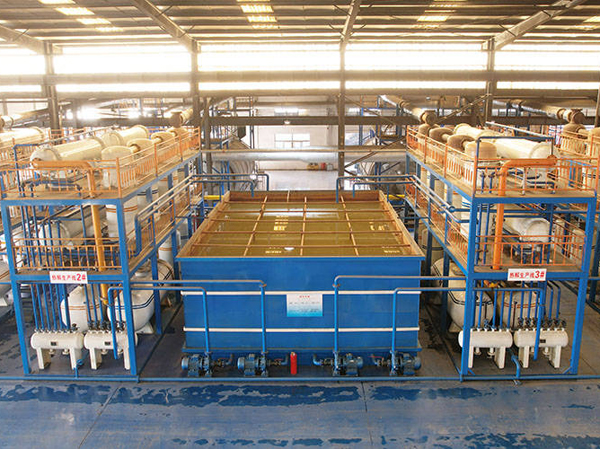
Usine de pyrolyse de pneus usagés
Le processus principal de l’usine de pyrolyse d’huile de pneus usagés comprend le prétraitement, le chauffage, le craquage, la condensation et la collecte. L’étape de prétraitement consiste principalement à réduire le pneu usagé en petits morceaux pour le chauffage et le craquage ultérieurs. Le processus de chauffage et de craquage est au cœur de l’ensemble du processus et nécessite l’utilisation d’équipements professionnels pour le craquage à haute température. Le processus de condensation et de collecte consiste à refroidir et à collecter le produit du craquage afin d’obtenir l’huile requise.
Dans ce processus, différents fabricants d’équipement peuvent utiliser différentes combinaisons de processus et d’équipement, de sorte que l’efficacité de l’équipement varie. En général, un équipement de haute qualité peut traiter les pneus usagés plus efficacement, obtenir plus d’huile et garantir la qualité de l’huile.
En outre, la stabilité de l’équipement est également très importante. Un bon équipement doit être très fiable, avoir une longue durée de vie et continuer à fonctionner de manière stable. Si l’équipement tombe fréquemment en panne ou nécessite une maintenance fréquente, l’efficacité opérationnelle et le coût de production de l’équipement s’en trouveront affectés.
Le processus de raffinage de l’huile de pyrolyse de pneus usagés est divisé en trois types : le type continu automatique, le type semi-continu, le type intermittent, etc. Quel que soit l’équipement de fabrication d’huile de pneu ci-dessus, il se compose principalement d’une bouilloire de réaction, d’un réservoir tampon, d’un système de condensation, d’un séparateur huile-eau, d’un joint d’étanchéité, d’une tour de désulfuration, d’un système d’élimination des scories, d’un four à huile thermique, d’un dispositif de pression négative, etc. Les détails de la configuration de l’équipement peuvent être ajustés en fonction de la taille de la capacité de traitement, du budget d’investissement, de l’échelle d’investissement et d’autres besoins.
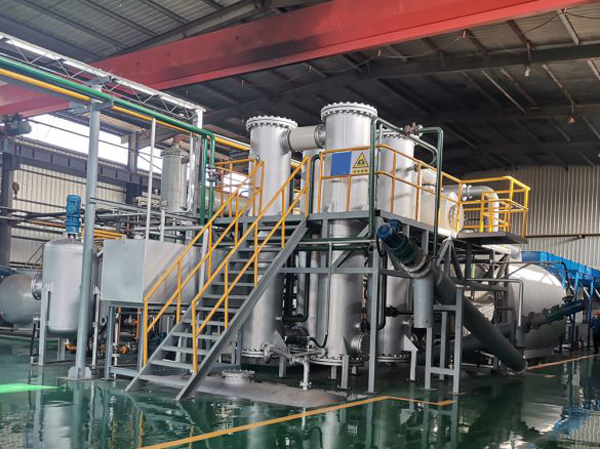
Procédé de fabrication par pyrolyse intermittente de pneus usagés
condenseur à colonne : deux condenseurs verticaux, chacun avec quatre tubes 108 à l’intérieur, et deux condenseurs horizontaux avec 38 tubes sans soudure à l’intérieur.
5) Méthode d’évacuation des scories : Décharge latérale des scories, qui doivent être refroidies avant d’être déchargées.
aucun prétraitement n’est nécessaire, le pneu entier peut être directement introduit dans la cuve de réaction.
méthode de chauffage : chauffage direct
efficacité de production : un four par jour

Processus de fabrication par pyrolyse semi-continue de pneus usagés
Condenseur à colonne : deux condenseurs verticaux, chacun avec quatre tubes de 108 à l’intérieur, et deux condenseurs horizontaux avec 38 tubes sans soudure à l’intérieur.
5) Méthode d’évacuation des scories : Peut évacuer les scories à haute température
Le traitement préalable consiste à broyer les pneus en poudre de caoutchouc de 16 à 18 mesh à l’aide d’une machine à broyer.
méthode de chauffage : chauffage direct
efficacité de la production : Trois fours en deux jours

Procédé de fabrication par pyrolyse en continu de pneus usagés
efficacité de la production : Peut produire en continu pendant plus de 40 jours, 24 heures sur 24, sans interruption
4.Condenseur à colonne : 3 réservoirs de condenseur tampon, 3 condenseurs verticaux (chacun avec plus de 30 tuyaux)
5.Méthode d’évacuation des scories : Technologie de scellement des matériaux, qui permet d’évacuer les scories en continu.
Un prétraitement est nécessaire pour broyer les pneus en poudre de caoutchouc de 16 à 18 mesh à l’aide d’une machine à broyer.
méthode de chauffage : chauffage indirect
La machine à huile de raffinage par pyrolyse des pneus usés peut être divisée en trois types en fonction de leurs modes de fonctionnement: intermittent, semi continu et continu. Alors, quelles sont les différences entre ces trois types d’équipement d’affinage de pneus usés et comment devraient-ils être sélectionnés
L’équipement de pyrolyse des pneus de déchets intermittente aliment directement l’ensemble du pneu dans le processus de raffinage, avec une capacité de traitement quotidienne de 1 à 15 tonnes. Actuellement, les équipements les plus couramment utilisés par les clients sont de 10 tonnes, 12 tonnes et 15 tonnes. Les dimensions extérieures, la capacité de traitement et l’équipement intermittent des équipements d’affinage semi-continu sont les mêmes, mais la différence réside dans l’amélioration des extrémités d’entrée et de sortie. La première extrémité excellente du matériau a été changée d’une grande porte de four à une spirale, ce qui signifie que l’alimentation ne peut être que des blocs de poudre de caoutchouc. Si c’est un pneu entier, il doit être écrasé et moulu pour le pré-traitement. L’extrémité de sortie adopte une décharge de laitier en spirale refroidie à l’eau, qui peut atteindre une décharge de laitier à haute température à 200 ° C, tandis que l’équipement d’affinage intermittent ne peut émettre de laitier que lorsque le four est abaissée à moins de 70 ° C, de sorte qu’il améliorera efficacement l’efficacité de la production. Selon les mêmes spécifications et tailles, l’équipement d’affinage intermittent des pneus usés ne peut affiner qu’un seul four par jour, tandis que l’équipement d’affinage semi-continu peut affiner trois fours en deux jours.
L’équipement d’affinage par pyrolyse continue des pneus usés est actuellement un excellent procédé sur le marché, avec une capacité de traitement quotidienne de 20 à 50 tonnes et une entrée d’alimentation en spirale. Contrairement aux équipements intermittentes et semi-continus, toute la ligne de production fonctionne en continu, sans devoir procéder à des arrêts fréquents, à des opérations d’ouverture et de fermeture des équipements, à des opérations de refroidissement et de réchauffage. Il peut accomplir la décharge de laitier et d’huile, et peut fonctionner sans interruption pendant environ 45-60 jours. Le four est arrêté une fois par jour pour l’entretien, ce qui le rend plus automatisé, intelligent et continu.
Indice technique de l’usine de raffinage d’huile de pyrolyse de pneus usagés
Article: | Détails détails | ||
Matière première traitable | Pneu usé, caoutchouc usé, plastique usé, plastique usé en aluminium, boue, résidu de goudron de charbon, déchets médicaux, déchets solides urbains, etc. | ||
Produit Final | Mazout, noir de carbone, fil d’acier, gaz combustible, laitier d’aluminium, asphalte, etc. | ||
Spécifications et modèle | Capacité de traitement (tonnes/jour) | Taille du four principal (m) | Power (KW) |
ZH-10 | 10 tons/day | Φ 2.6, H 6.6 | 5KW |
ZH-12 | 20 tons/day | Φ 2.8, H 6.6 | 5KW |
ZH-15 | 15 tons/day | Φ 2.8, H 8.6 | 8KW |
ZH-18 | 18 tons/day | Φ 3, H 8.6 | 12KW |
ZH-20 | 20 tons/day | Φ 3, H 8.9 | 12KW |
ZH-50 | 50 tons/day | Φ 3.6, H 10 | 20KW |
ZH-100 | 100 tons/day | Φ 5, H 13 | 35KW |
Working form | Intermittent, continuous | ||
Structural design | ① four rotatif Horizontal ② équipement rotatif interne, la rotation intérieure du réservoir de four de fissuration, le matériel à travers le dispositif de guide à l’intérieur du four de fissuration pour promouvoir le matériel d’une extrémité à l’autre extrémité courent uniformément, afin de compléter l’opération entière | ||
Matériau du réacteur | Q345R/Q245R/ Boiler plate +/304/316 acier inoxydable | ||
thickness | 15 mm /16 mm /19 mm | ||
Méthode de chauffage | Chauffage Direct, chauffage indirect | ||
Combustible de chauffage | Pétrole, gaz, charbon, bois, etc. | ||
Type de refroidissement | Refroidissement à l’eau en circulation | ||
Espace machine | Prenez une machine de 15 tonnes par exemple, 600 mètres carrés | ||
Travailleurs nécessaires | 2-3 | ||
Émission de gaz de combustion | Atteindre la norme |
Principe technique de l’usine de pyrolyse des pneus usés
Le processus de base de l’équipement d’affinage des pneus usés est le traitement par pyrolyse à basse température. Les pneus sont principalement composés de caoutchouc (y compris le caoutchouc naturel, le caoutchouc synthétique), de noir de carbone et de divers additifs organiques et inorganiques (y compris des plastifiants, des agents anti-âge, du soufre et de l’oxyde de zinc). La plupart des composés organiques ont des caractéristiques d’instabilité thermique. S’ils sont placés dans des conditions anaérobies et à haute température, sous l’action combinée de la décomposition et de la condensation, les grands composés organiques moléculaires subissent des craquelures et se transforment en composants gazeux, liquides et solides de poids moléculaire relativement faible.
La fissuration thermique des pneus usés est un processus de réaction chimique complexe et continu. Cela comprend des réactions chimiques telles que la rupture de liaison, l’isomérisation et la condensation de petites molécules, entraînant finalement la formation de molécules plus petites. Au cours du processus de pyrolyse, il y a deux tendances dans les produits intermédiaires: l’une est la transformation de grandes molécules en petites molécules, jusqu’à ce que le gaz subisse la fissuration; Le second est le processus de polymérisation de molécules extrêmement petites en molécules plus grandes. Cette réaction n’a pas un stade clair, et de nombreuses réactions se produisent croisées. Le procédé de pyrolyse peut s’exprimer comme suit: déchets solides organiques → gaz (H2, CH4, CO, CO2)+ liquides organiques (acides organiques, aromatiques, goudron, kérosène, alcools, aldéhydes, etc.)+ solides (noir de carbone, laitier).
Procédé de travail usine de pyrolyse des pneus usés
La principale matière première traitée par l’équipement d’affinage des pneus usés est des pneus usés propres achetés, qui ne nécessitent pas de processus de prétraitement tels que le nettoyage, le concassage et le tréfilage. Ils sont directement introduits dans le four à fissuration rotative sous l’action en spirale du four, et le processus d’alimentation est hautement automatisé, sûr, commode et gain de temps. Le flux de procédé spécifique pour le raffinage des pneus usés est le suivant:
Prétraitement des pneus
Pneu usé à travers la machine de tréfilage d’acier pour retirer le fil d’acier dans le pneu usé, puis mettre le pneu dans le broyeur de pneu. Après le traitement du broyeur de pneus, les pneus sont transformés en morceaux de 3-5 cm.
Alimentation des animaux
Tout d’abord, le travailleur conduit un chariot élévateur pour mettre les pneus usés dans la machine d’alimentation automatique. Une extrémité de la machine d’alimentation est reliée à la bouilloire à réaction de fissuration, et les pneus usés sont poussés dans la bouilloire à réaction de fissuration par la poussée de la tige hydraulique. Le temps d’alimentation est de 2-3 heures. Une fois la bouilloire à réaction de fissuration remplie de pneus usés, fermer la porte du four, s’enflammer et chauffer pour s’assurer que les pneus usés sont chauffés et fissurés dans des conditions fermées et sans oxygène.
Pyrolyse continue
Ensuite, pendant le processus de chauffage des pneus usés, il y aura un processus du solide au gaz, puis au liquide. Lorsque la température à l’intérieur du réacteur de pyrolyse atteint la température de pyrolyse du pneu (180 ℃), les liaisons macromoléculaires en caoutchouc dans le pneu se brisent et deviennent de petites molécules, commençant à se fissures et à libérer du gaz. Le pétrole et le gaz produits par pyrolyse pénètrent dans le réservoir tampon/séparateur, et le gaz se déplace de l’avant vers l’arrière. Après avoir traversé le réservoir tampon, le volume de pétrole et de gaz se dilate rapidement, le débit ralentit et les impuretés de noir de carbone transportées dans le pétrole et le gaz peuvent également se déposer au fond du réservoir.
refroidissement
Le pétrole et le gaz tampons entrent dans le premier système de refroidissement par le skytube – deux condenseurs verticaux parallèles. Les condenseurs verticaux sont constitués de quatre 108 conduites, entourées d’eau de circulation condensée. Le pétrole et le gaz échangent la chaleur avec l’eau condensée à travers les tuyaux. Après que la température du pétrole et du gaz diminue, il passe d’un état gazeux à un état liquide, et est converti en huile de craquage pour le stockage temporaire dans le réservoir d’huile. À l’avenir, le pétrole et le gaz condensés continueront à entrer dans les deuxième et troisième systèmes de refroidissement – séparateurs huile-eau et deux condenseurs horizontaux parallèles. Le principe de refroidissement des condenseurs horizontaux et verticaux est le même, mais leurs tuyaux de refroidissement sont plus et plus minces, et la zone d’échange de chaleur est plus grande. A ce stade, l’huile de craquage la plus condensée est produite.
Après avoir traversé les trois systèmes de condensation frontaux, près de 80 à 90% du pétrole et du gaz ont été condensés en huile. Cependant, notre entreprise a également mis en place un quatrième système de condensation – deux tours de condensation verticales. Le flux de pétrole et de gaz de bas en haut, avec un débit lent autant que possible, afin de refroidir le pétrole et le gaz générés autant que possible. En même temps, il peut également éviter un mauvais contrôle de la température pendant le processus d’allumage par le brûleur, ce qui entraîne une vitesse de production d’huile et de gaz trop rapide et un temps insuffisant pour le système de condensation avant de se condenser, ce qui entraîne une diminution du rendement en huile. Par conséquent, nous avons ajouté un dispositif de condensation pour augmenter la tolérance.
- Section épuration des gaz d’échappement
Les autres gaz non condensables mais très inflammables ne peuvent être récupérés par le système de condensation et pénètrent dans le dispositif de désulfuration et de désodorisation pour le traitement d’épuration. Le gaz non condensable s’écoule de bas en haut, et après avoir été uniformément dispersé par l’emballage, il subit une réaction chimique approfondie avec la solution d’hydroxyde de sodium alcalin. La fusion acide-base éliminera les gaz tels que le sulfure d’hydrogène, le dioxyde de soufre et le monoxyde de soufre du gaz non condensable. Le gaz non condensable après désulfuration et désodorisation est renvoyé dans le réacteur de craquage comme combustible pour le chauffage.
Section d’épuration des gaz de combustion
Les gaz de combustion poussiéreux générés lors de la combustion des gaz non condensables et du processus d’affinage des pneus usés entreront dans la tour de désulfuration et de désodorisation. Le gaz de combustion poussiéreux circule de bas en haut et est uniformément dispersé par quatre pulvérisations et quatre couches de charges en céramique. Par pulvérisation couche par couche, le gaz est mélangé et réagit avec la solution d’alcali pour réaliser la désulfuration. Les particules de poussière sont séparées par la force centrifuge et les particules de fumée sont adsorbées par la couche de film d’eau générée par la pulvérisation. Ils s’écoulent avec l’eau vers le cône inférieur et sont évacués par la sortie de poussière pour atteindre l’objectif de dépoussiérage.
- Section de déchargement des scories
Une fois la fissuration terminée, ouvrir la pression négative sous vide et continuer à travailler pendant une demi-heure pour éliminer les résidus d’huile et de gaz à haute température dans la bouilloire à réaction, réduire la concentration d’huile et de gaz, et éviter l’explosion instantanée lors de l’ouverture de la porte du four et de l’entrée en contact avec l’oxygène. Fermer de nouveau le système de chauffage, ouvrir le ventilateur de tirage induit et les 4 soupapes d’entrée d’air. Le ventilateur à tirage induit extrait l’air chaud du four, et l’air froid entre par l’entrée d’air pour obtenir un refroidissement rapide et un refroidissement du four. L’utilisation du système d’air froid pour refroidir le four prend 4 à 5 heures, ce qui permet d’économiser la moitié du temps.
Après la baisse de température du four, le système d’évacuation des scories peut être ouvert pour l’évacuation des scories. En utilisant la méthode de décharge latérale des scories, un orifice de décharge des scories est ouvert tous les 180 degrés à l’arrière du four, et les scories sont déchargés deux fois pour chaque rotation. La bouilloire réactionnelle tourne dans le sens opposé et le noir de carbone est évacué de l’orifice d’évacuation des scories. Le temps de sortie des scories est de 2 à 3 heures.
- Section de traction de fil
Après la sortie des scories grossières de noir de carbone, il ne reste plus que la section de traction du fil. La section de traction de fil sort le fil brut à l’intérieur de la bouilloire à réaction et le recueille uniformément. Enfin, recueillir l’huile fissurée du réservoir de stockage temporaire de l’équipement dans le grand réservoir de stockage de l’huile sur place.
- Collection de produits pétroliers
L’huile liquide est recueillie dans le réservoir. Pas de feux d’artifice autour du réservoir d’huile.
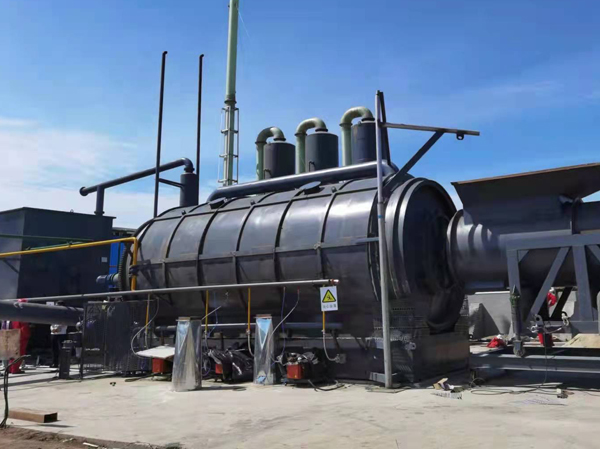
Couche spéciale d’isolation avec le bon effet d’isolation
Le réacteur principal est en acier de chaudière standard

Alimentation compacte, vitesse d’alimentation rapide, capable de l’alimentation à haute température
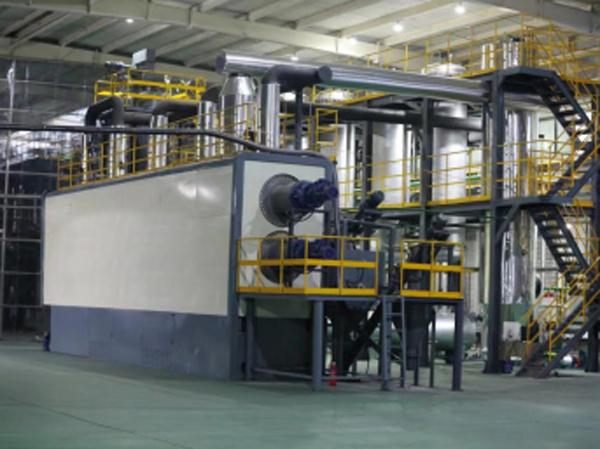
Le noir de carbone déchargé par haute température est refroidi dans ce réacteur et stocké après avoir atteint une certaine température
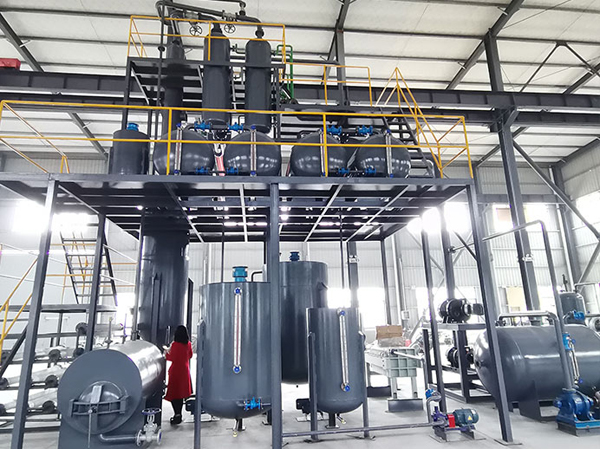
Le condenseur de type boîte de conception unique apprécient un bon effet de refroidissement et facile à nettoyer.
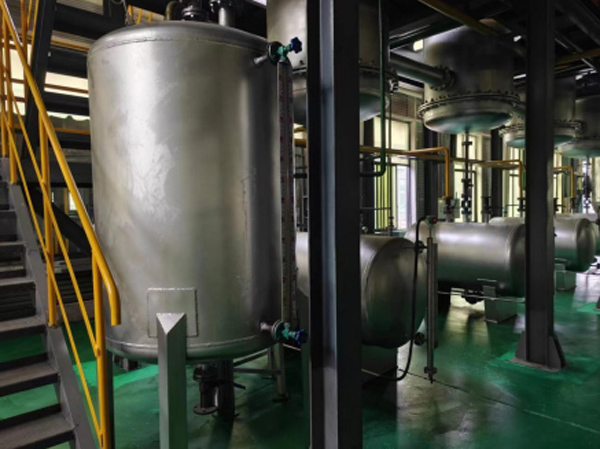
Système de recyclage de gaz combustible Non condensable recyclant en toute sécurité les gaz résiduaires dans la chambre de combustion pour brûler pour économiser le carburant
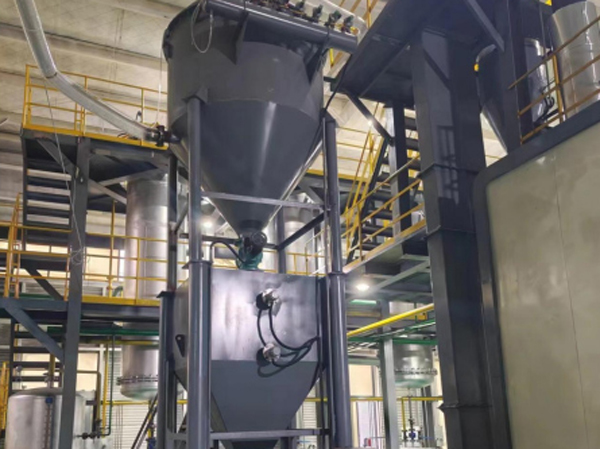
Purifier les gaz d’échappement générés par la combustion et les rejeter après avoir satisfait aux normes d’émission.
Technologie de l’usine de pyrolyse continue des pneus usés
Notre usine de pyrolyse a le système d’alimentation automatique. Le matériau passe de la souterraine à l’alimentateur et passe ensuite dans le réacteur, qui fonctionne automatiquement. Et aucune poussière volante dans l’atelier du tout.
Nous avons une technologie d’économiser l’énergie: le combustible est chauffé au fond du réacteur indirectement (flamme vers le sol), avec 8 brûleurs installés uniformément sur le réacteur, qui peuvent transférer l’énergie thermique de manière égale au réacteur tout autour à 360 degrés. De cette façon, il permettra d’économiser beaucoup d’énergie de combustible et de protéger le réacteur pour une durée de vie plus longue.
A l’heure actuelle, le plus gros problème pour la production continue de réacteurs rotatifs est la cokéfaction épaississante qui se forme en continu lorsque les matériaux d’alimentation sont affectés par des températures élevées dans le réacteur, ce qui non seulement rend la réaction impossible à poursuivre, mais endommage aussi rapidement l’équipement. Nous avons une technologie de pointe spéciale qui peut constamment enlever le coke dans le réacteur pour assurer l’alimentation continue et la pyrolyse qui prolongera considérablement la vie de l’équipement et augmentera également l’efficacité de la production.
Pendant le processus de chauffage, le réacteur tournera automatiquement et lentement, régulièrement 3 minutes par tour, le matériau se pyrolyse complètement après d’une extrémité à l’autre extrémité. Et la qualité de noir de carbone sont beaucoup mieux avec la teneur en huile moins de 0,3% seulement. La qualité du noir de carbone est une poudre fine.
Le gaz syn généré par le système sera utilisé pour soutenir le chauffage continu. Le système entièrement continu même dose pas besoin de carburant supplémentaire une fois le système est démarré. Parce que le gaz syn sera assez loin pour le chauffage. Il permettra d’économiser une grande partie du coût du carburant.
6, technologie élevée de rendement d’huile. Généralement, il y a encore une grande quantité de gaz syn repos après la combustion, nous avons la technologie pour convertir le gaz syn en mazout à nouveau, ainsi il augmentera le taux de rendement d’huile à 42-48% (taux régulier autour de 40% seulement).
Avec notre technologie spéciale d’étanchéité douce, l’ensemble de l’usine de pyrolyse est totalement étanche à l’air sans problème de fuite. Ainsi il n’y a aucun gaz nocif ou mauvaise odeur sortant du système. Et le système a une valve de dépressurisation automatique, de sorte que la pression à l’intérieur du réacteur ne sera jamais dangereuse.
Tout le système de collecte en noir de carbone et en fil d’acier recouvert d’un système étanche à l’air et connecté à l’équipement de collecte de la poussière. Ainsi, tout l’atelier sera bien rangé et avec moins de bruit.
Nous utilisons des piscines d’eau uniquement pour le refroidissement (pas de N2). L’eau est utilisée circulairement de l’équipement dans la piscine, ce qui permettra d’économiser beaucoup de coût par jour.
Système de décharge muti-gradué avec l’eau jacked basse température de promesse tout en déchargeant.
Tout notre système a passé les certificats ISO,SGS et CE.